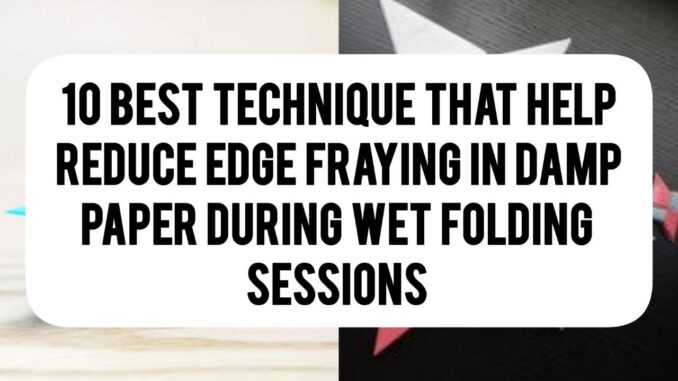
Edge fraying is the bane of wet‑folding enthusiasts worldwide. That telltale “fuzz” distracts from your smooth curves and crisp details, turning hours of precision work into a battle against unruly fibers. But here’s the good news: with the right know‑how, you can transform your paper into a disciplined partner. This article will dive deep—really deep—into ten powerhouse techniques, plus bonus tips, to keep edges tight, tidy, and totally under your control. By the end, you’ll have a toolbox brimming with strategies to tackle any wet‑folding challenge that comes your way.
Why does paper fray when it’s damp?
The science behind fiber swelling
At its core, paper is a mesh of tiny cellulose fibers. When you introduce moisture, those fibers swell like sponges, pushing against one another and loosening the bonds that held them snug. On a smooth surface, these swollen fibers can align into a unified sheet. But along a cut edge, there’s no backing to keep them in place, so they splay out, creating that dreaded frayed margin.
Mechanical stress from folding
Wet‑folding isn’t just about adding water; it’s about transforming flat paper into sculptural forms through bending, stretching, and compressing. Each fold applies mechanical stress to the fibers—especially at corners and along edges—exacerbating fraying. Think of twisting a damp towel: the edges begin to unravel under tension.
Materials you’ll need to tame fraying
selecting the ideal paper weight
Not all papers are equal. Lightweight 60–80 gsm printing paper will quickly disintegrate, while extremely heavy cardstock resists folding altogether. Aim for mid‑weight stocks—100–160 gsm—often labeled “origami,” “watercolor,” or “multimedia.” These papers balance flexibility with fiber density, giving you enough strength to resist fraying while still allowing gentle shaping.
gathering your wet‑folding arsenal
Beyond paper, assemble a few key tools:
- A fine‑mist spray bottle for even dampening
- A soft watercolor brush to direct moisture precisely
- A bone folder or smooth spoon handle for crisp creases
- A microfiber cloth for blotting excess water
- PVA glue, acrylic medium, or diluted bamboo paste for sealing edges
With these at hand, you’ll be primed to apply each technique to maximum effect.
technique 1: pre‑treating edges with a water‑resistant sealant
why sealants act like tiny shields
Imagine your paper edges donning minis raincoats. A thin coat of PVA glue or acrylic medium forms an invisible barrier, preventing water from infiltrating the fiber matrix. That protective film helps fibers stay anchored, even under the pressure of wet‑folding.
detailed application method
First, mix plain PVA glue with an equal part of water in a small container. Dip a fine brush into the mixture and paint a fine line along each edge, avoiding the interior surfaces. Let the sealant dry until tacky—about 5–10 minutes—before misting the paper. This delay ensures the glue forms a flexible skin, not a stiff shell. When you fold, those edges won’t fuzz out, and your model’s silhouette stays sharp.
technique 2: using a soft brush for moisture control
targeted dampening over indiscriminate spraying
A spray bottle is perfect for quick work, but direct misting often soaks edges. Instead, load a soft watercolor brush with filtered water. Brush the liquid gently into fold zones, steering clear of cut perimeters. By localizing moisture where you need pliability—and sparing fragile edges—you preserve fiber integrity.
mastering the brush stroke
Hold the brush almost parallel to the paper, lightening your grip. Feather the water onto valley and mountain folds, as though painting vines on a canvas. The whispered touch keeps edges drier while giving the core enough hydration to sculpt curves.
technique 3: edge rolling to compress fibers
how rolling locks fibers in place
Once fibers swell, lightly rolling an edge compresses them back together. Think of it like ice skating on a freshly Zamboni’d rink: each pass smooths the surface. Rolling creates friction that re‑bonds fibers, resisting further separation.
step‑by‑step rolling guide
After dampening, use a rounded tool—such as the handle end of a paintbrush or a smooth dowel—press lightly against the edge. Roll along its entire length with gentle, even pressure. Repeat both before and after primary folds. This technique gives edges a polished firmness, like the finished rim of a paper cup.
technique 4: blending wet and dry folding phases
the rhythm of alternating moisture
Instead of going full‑wet from start to finish, stagger your workflow. Begin with all major structural folds while the paper is dry—this lays the skeleton. Next, mist for softer curves. Finally, let sections dry completely before tackling intricate details. Similar to cooking a soufflé, you need staged temperature control to avoid collapse.
crafting your fold timeline
Map your design into zones: base creases, shaping folds, and fine details. Follow a three‑phase protocol: dry initial shaping, wet curvature sculpting, dry detail work. This choreography minimizes fiber fatigue, reserving moisture for moments where it’s truly needed.
technique 5: edge cropping for precision
why a clean cut matters
If your paper’s raw, uneven edges show damage from manufacturing or handling, fraying becomes inevitable under wet‑folding. Think of it like sewing—starting with jagged fabric edges leads to frayed seams.
precision trimming technique
Using a sharp X‑Acto blade and metal ruler, slice away ragged margins in one confident pass. Always cut on a self‑healing mat. The result? A pristine edge that stands up to water and folding, just like a well‑trimmed hedge holds shape better than a wild thicket.
technique 6: reinforcing corners with fiber patches
spot‑treating high‑stress hotspots
Corners accumulate stress during multiple folds, making them fray first. By patching with tiny paper reinforcements, you shore up these weak points.
corner patch application
Tear off micro‑flakes of the same paper, moisten them, and dab with diluted glue. Position them on inside corners, smoothing them flush. As they dry, the patch fibers weave into the base sheet, creating a composite that resists edge splitting.
technique 7: using controlled humidity environments
why workshop climate influences fiber behavior
Ambient humidity affects how quickly your paper gains or loses moisture. Too dry, and folds crack; too humid, and edges stay soggy and prone to fraying.
setting up your folding “microclimate”
Place a small hygrometer on your work surface. If the air is below 40 percent relative humidity, run a compact humidifier nearby. Above 60 percent, use a dehumidifier or switch on air conditioning. Maintaining this sweet spot ensures predictable fiber response, akin to marinating meat at the ideal temperature.
technique 8: employing wax or paraffin edge treatment
water‑repellent coating for ultimate defense
Waxing edges forms a hydrophobic barrier—water beads and rolls off, never soaking in. This is the same principle that lets candle-waxed seams shrug off rain.
wax application steps
Lightly warm a paraffin block or candle, and hold it about an inch from each edge. The melted wax lightly coats the perimeter. Buff excess with a soft cloth until the edges feel sleek but not greasy. Your paper will repel water much like a duck’s feathers.
technique 9: strategic folding order to minimize stress
planning fold sequences for fiber longevity
The sequence in which you make folds affects how stresses accumulate. Complex crumple‑folds early can weaken edges before you get to finer shaping.
fold path optimization
Create a step chart: broad structural creases first, followed by intermediate forms, and finally detailed sculpting. Treat each edge region like a relay team—only pass the baton (stress) when previous runners (folds) have had time to “recover” (partially dry). This keeps fibers from tiring too soon.
technique 10: post‑fold edge finishing
final sealing for showroom‑ready models
After your model dries completely, give edges one last protective wash: a thin layer of diluted PVA or acrylic varnish. This topcoat cements fibers and guards against handling wear, much like a clear auto lacquer protects a car’s paint.
application and drying protocol
Using a superfine brush, trace the perimeter with one fluid stroke. Allow a full 12 hours for air drying on a flat surface. Avoid forced heat, which can warp delicate forms. Your model’s edges will emerge gleaming, sharp, and utterly fray‑proof.
additional tip: choosing complementary paper blends
blended‑fiber stocks for optimal performance
Cotton/wood‑pulp blends marry the tensile strength of cotton with the affordability of wood pulp. The cotton fibers act like reinforced bars in concrete, holding the pulp in place when wet.
commercial wet‑folding papers to explore
Brands such as Tant by Moriki, Clarkson, and Elephant Hide are favorites in wet‑folding circles. They offer consistent fiber distribution and sizing that resists over‑absorption. Sampling a variety helps you find that perfect sheet for your style.
addressing tool maintenance and hygiene
keeping brushes in peak condition
Leftover glue, paste, or pigment can stiffen bristles and leave streaks. Rinse brushes immediately in warm water, reshape with your fingers, and hang bristles down to dry. Fresh brushes mean cleaner sealant lines and more precise folding.
storing blades, rulers, and dowels safely
Keep cutting blades capped, metal rulers in a cloth sleeve, and rolling tools in a padded compartment. Organized tools save time and prevent accidental nicks that create jagged edges—even before you start.
troubleshooting common fraying scenarios
mid‑project fraying attack
If edges begin to fuzz, pause. Let the sheet dry fully, then apply a quick wax rub or diluted sealant coat. Lightly roll again, and you’ll restore integrity before continuing.
persistent edge fuzz despite precautions
Reevaluate your moisture application. You may need to dial back water volume or switch to brush dampening. Over‑wetting often lies at the heart of stubborn fraying.
balancing artistic expression and technical control
when a little fray adds character
Not every project demands razor‑sharp edges. Soft fraying can lend a weathered, vintage look—ideal for antique props or abstract pieces. Embrace texture intentionally, rather than fighting every fiber.
knowing your perfection threshold
Set realistic goals per project. A hyper‑detailed animal sculpture might justify ten treatment steps, while a simple blossom motif benefits from fewer interventions. Choose methods that serve your vision, not distract from it.
why mastering edge control elevates your wet‑folding
enhancing model durability
Edge‑tamed pieces survive display, handling, and occasional dusting. They become heirloom‑quality works of art rather than delicate experiments.
boosting professional presentation
For commissioned or exhibition pieces, crisp, unfrayed edges signal professionalism and craftsmanship. Clean edges are the final punctuation mark on a beautifully folded sentence.
conclusion
Edge fraying in damp paper is a predictable challenge—but it’s also one you can outsmart. By weaving together pre‑treatments, controlled moisture application, precise folding sequences, and thoughtful post‑fold finishes, you’ll tame those zebra‑striped edges into polished, professional margins. Whether you’re sculpting lifelike creatures, elegant garments, or architectural marvels in paper, these ten techniques (plus bonus tips) give you total command over fiber behavior. Embrace the science, rehearse the choreography, and let your creativity run wild—now with perfectly obedient edges.
FAQs
how often should i reapply sealant to edges?
For intensive wet‑folding where multiple water exposures occur, reapply a light coat of diluted PVA after each major fold phase. In simpler projects, one pre‑treatment and one post‑treatment usually suffice.
can i use natural alternatives like rice paste instead of PVA?
Yes. Traditionally, rice or wheat starch pastes serve as flexible sealants. They offer similar fiber binding but require careful cooking and straining to avoid lumps.
will wax treatment darken or discolor bright papers?
On most light‑colored papers, paraffin leaves a subtle sheen but no visible darkening. Always test on a small scrap to confirm the aesthetic outcome.
is it better to trim edges before or after the first wet fold?
Trim before any moisture hits the paper. Wet trimming risks tearing larger sections and exacerbates fiber separation.
my paper still frays despite all techniques—what am I missing?
Recheck your humidity levels and moisture application method. Even high‑end papers will fray if you accidentally drench edges. Focus on precise brush dampening and consider adding one more sealant layer.
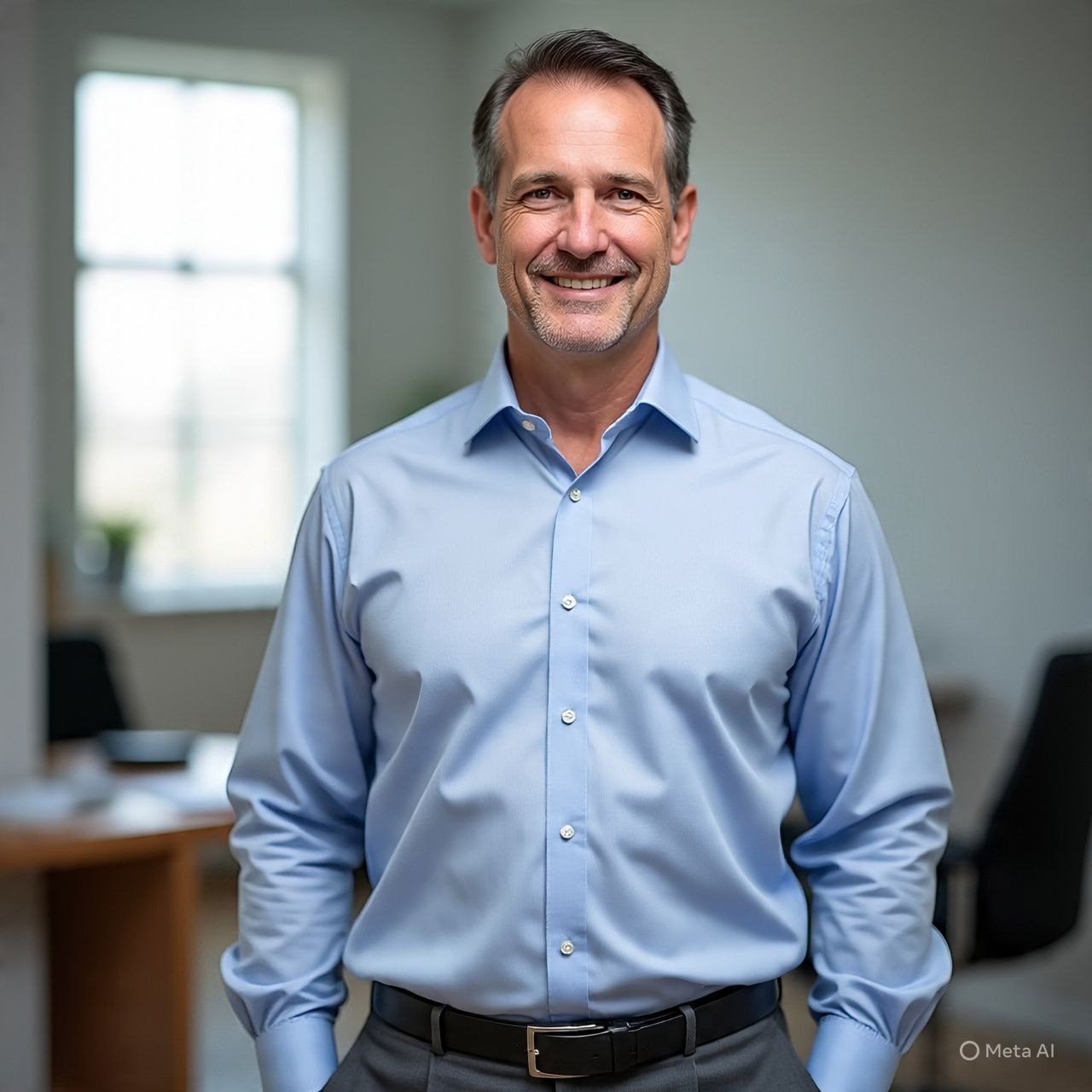
Donald George holds both a Bachelor’s and a Master’s degree in Fine Arts and has spent the past decade honing his craft in Astrophotography and Origami. He has authored numerous academic papers on astrophotography techniques and the art of paper folding, and his work is frequently cited in specialist journals. With ten years of hands‑on experience, Donald combines his artistic vision and technical expertise to push the boundaries of both traditional fine art and Astrophotography.
Leave a Reply